Aug 11, 2025
In the restoration industry, air scrubber repair often takes a backseat to acquiring new equipment or managing current projects. However, this oversight can cost restoration companies thousands of dollars annually in unnecessary expenses, reduced efficiency, and shortened equipment lifespan.
At First Choice Drying Equipment, we’ve seen countless restoration professionals transform their bottom line simply by implementing regular maintenance and repair protocols for their air scrubbers. With our help, you can maximize equipment longevity, reduce unexpected breakdowns, and deliver superior results to your clients.
Why Air Scrubber Repair Matters to Your Bottom Line
Air scrubbers represent a significant capital expenditure for restoration companies, with high-quality units costing thousands of dollars. When properly maintained, an air scrubber can provide reliable service for 7-10 years or more. Without regular maintenance, that timeframe can be cut in half, forcing you to replace equipment prematurely and draining your company’s financial resources.
Common Air Scrubber Issues That Regular Maintenance Prevents
Many costly air scrubber repairs begin as minor issues that, if caught early, would require minimal intervention. Look out for these common problems:
Clogged Filters
Filters are the workhorses of your air scrubber, and they’re designed to capture particles and contaminants. Over time, these filters become clogged, forcing your machine to work harder to maintain the same airflow. Increased airflow strain leads to higher energy consumption and puts stress on the motor and other components.
A clogged primary filter can reduce airflow by up to 50%, significantly decreasing the effectiveness of your air scrubbers on job sites. Regularly replacing filters costs a fraction of what you’ll spend on increased operation time or premature motor repairs.
Motor Burnout
When filters clog and airflow becomes restricted, your air scrubber’s motor has to work overtime. This additional strain generates more heat and accelerates wear and tear on motor components. The result? Premature motor burnout and lost revenue from equipment downtime.
Regular maintenance allows technicians to identify signs of motor stress before catastrophic failure occurs. Simple interventions like cleaning cooling fins, checking electrical connections, and ensuring proper lubrication can prevent expensive air scrubber repair and keep your equipment running smoothly.
Housing Damage
The external housing of your air scrubber might seem like a purely cosmetic concern, but cracks, dents, or loose components can significantly impact performance. Damaged housing can allow unfiltered air to bypass the filtration system, reducing efficiency and potentially releasing contaminants back into the environment.
Regular inspection of your air scrubber’s housing ensures that the unit maintains proper air pressure and flow patterns. Catching small cracks or seal issues early will save your equipment from internal component damage or premature replacement.
The Hidden Costs of Neglecting Air Scrubber Maintenance
Beyond the obvious expense of replacement parts and repair labor, neglecting air scrubber repair creates several hidden costs that many restoration companies fail to account for in their financial planning.
Project Delays and Deadline Extensions
When an air scrubber fails mid-project, your project timeline extends, potentially incurring contractual penalties or damaging client relationships. A single day of project delay can cost a restoration company $500-$2,000 in labor, overhead, and opportunity costs. Regular air scrubber repair will dramatically reduce the risk of unexpected equipment failure, helping you maintain tight project schedules and client satisfaction.
Increased Energy Consumption
A poorly maintained air scrubber requires significantly more power to operate at capacity. Although increased energy consumption may seem negligible on a day-to-day basis, it adds up quickly across multiple units and projects.
Studies show that well-maintained HVAC and air filtration equipment can operate up to 30% more efficiently than neglected units. For a restoration company running multiple air scrubbers across various job sites, this efficiency could save you thousands of dollars in annual energy costs.
Diminished Air Quality Outcomes
The primary purpose of an air scrubber is to improve air quality by removing contaminants. When these machines operate below optimal efficiency due to maintenance issues, they fail to achieve the air quality standards you expect and fail to meet guidelines. Substandard air quality outcomes can lead to failed inspections, client complaints, and even potential liability issues in sensitive environments where GSA-approved products are required.
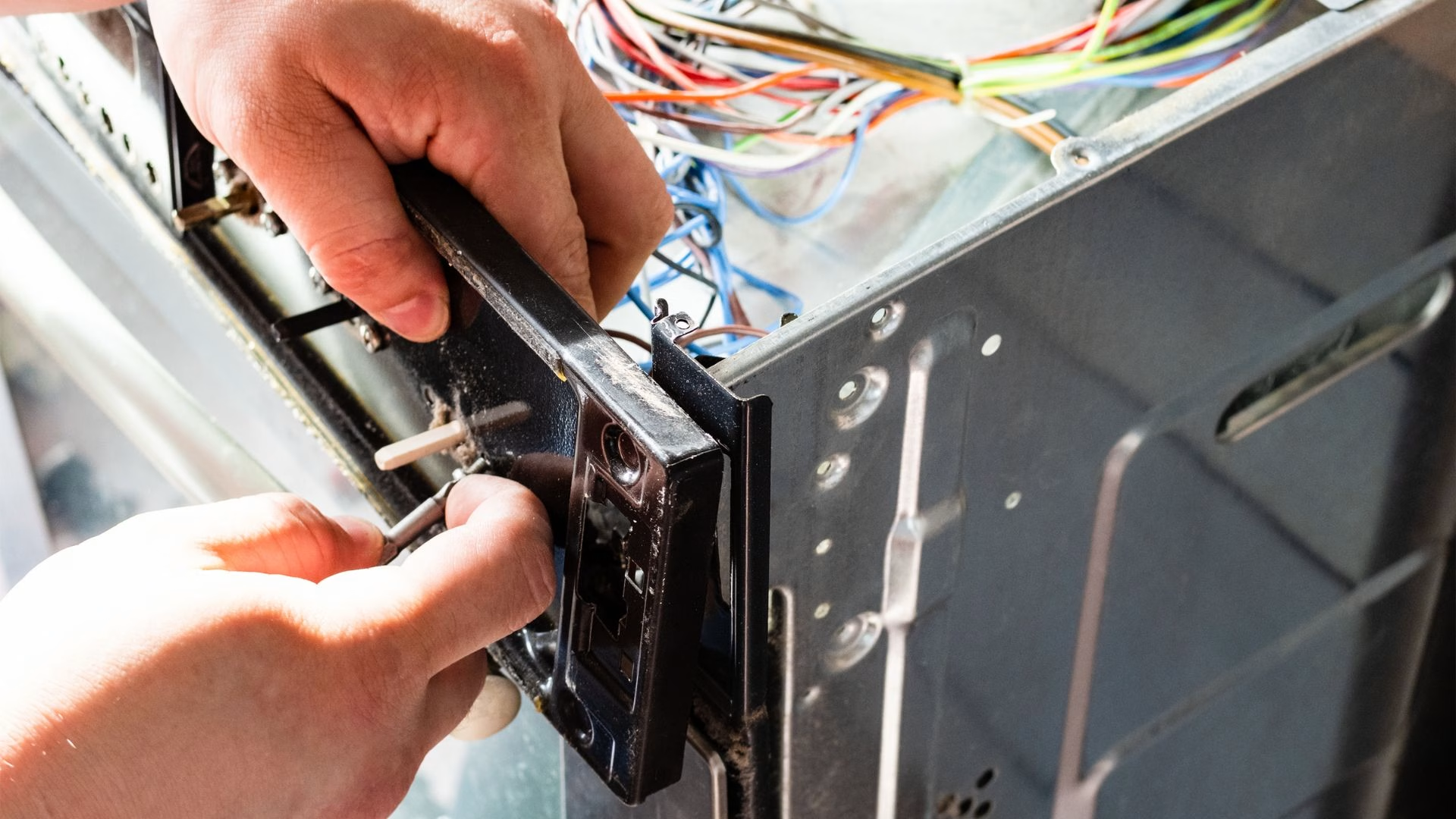
Developing a Cost-Effective Air Scrubber Maintenance Schedule
Implementing a strategic maintenance schedule transforms air scrubber repair from a reactive expense to a proactive investment. Here’s how to develop a maintenance program that maximizes savings and minimizes downtime:
Create Equipment History Logs
Maintain detailed service records for each air scrubber in your fleet. These logs should document:
- Purchase date and original specifications
- All maintenance and repair activities with dates
- Parts replaced and their costs
- Performance testing results
- Unusual observations or recurring issues
History logs allow you to identify patterns, anticipate needs, and make data-driven decisions about air scrubber repair versus replacement.
Daily Operator Checks
Train your field technicians to perform basic daily checks on air scrubbers before and after each use. Have operators check for unusual noises, vibrations, or odors during operation. They should also visually inspect filters for excessive soiling, examine power cords for damage, and ensure all controls function properly. Documenting these checks creates accountability and helps track equipment performance over time.
Monthly Deep Cleaning and Inspection
Dedicate time each month to a more thorough cleaning and inspection of your air scrubber fleet, including:
- Thoroughly cleaning exterior surfaces and air intake areas
- Inspecting and cleaning pre-filters and primary filters
- Checking all electrical connections and components
- Examining housing seals and gaskets for leaks
- Testing airflow performance against manufacturer specifications
Monthly sessions typically require 30-60 minutes per unit, but catch many common failures before air scrubber repair is necessary.
Quarterly Professional Service
Even with diligent daily and monthly maintenance, professional service from a company like First Choice is needed to maximize equipment longevity. At your quarterly service appointments, qualified technicians:
- Conduct comprehensive diagnostic testing
- Address minor issues before they become major problems
- Perform preventative replacements and air scrubber repair
- Calibrate sensors and controls for optimal performance
- Update equipment with any manufacturer-recommended modifications
Read Also: Expert Repairs on Restoration Equipment with First Choice
How First Choice Drying Equipment Can Help
At First Choice Drying Equipment, we specialize in helping restoration companies implement effective air scrubber repair and maintenance programs that maximize equipment value and minimize operating costs. Our comprehensive services include:
Expert Maintenance and Repair
Our certified technicians have extensive experience with all major air scrubber brands and models. We can diagnose issues quickly and provide cost-effective air scrubber repair using genuine parts. Our preventative service and repair programs are designed specifically for the demands of the restoration industry, addressing the unique challenges your equipment faces in varied work environments.
Quality Replacement Options
When air scrubber repair isn’t economical, we offer competitive pricing on air scrubbers and HEPA systems that will meet your specific needs. Our inventory includes various capacities and features, allowing you to select equipment that’s perfectly suited to your typical projects. We stand behind every unit we sell with exceptional service and support.
Rental Solutions During Repairs
We understand that downtime isn’t an option in the restoration business. That’s why we offer equipment rentals to keep your projects moving while maintenance or repair takes place. Our flexible rental terms accommodate both short-term emergency needs and longer-term project requirements.
Related: The Benefits of Renting vs. Buying Restoration Equipment: Making the Smart Choice
Training and Technical Support
Our commitment extends beyond equipment sales and service. We also provide comprehensive training for your staff on proper air scrubber operation and basic maintenance. Our technical support team is always available to answer questions and troubleshoot issues, helping you maximize the value of your equipment investment.
Need Air Scrubber Repair? Take Action Today with First Choice!
Don’t wait for equipment failures to disrupt your projects and drain your resources. Implementing a proactive air scrubber repair and maintenance program is investing in your company’s operational excellence and financial health. The thousands of dollars you’ll save represent resources you can redirect toward growth initiatives, employee development, or improved client services.
We want to discuss how our air scrubber maintenance and repair services can benefit your restoration company. Get in touch with First Choice Drying Equipment today by scheduling a consultation or by giving us a call. Your air scrubbers work hard for your business; make sure you’re protecting your investment with the care and attention it deserves.
Jul 14, 2025
When your restoration business depends on reliable equipment, finding a trustworthy air mover repair service becomes an integral step towards your operation’s success. At First Choice Drying Equipment, we understand that your air movers are the workhorses of your water damage restoration fleet, and keeping them running at peak performance isn’t just about maintenance; it’s about protecting your bottom line.
We’ve built our reputation on providing specialized repairs that address the unique challenges faced by disaster recovery professionals. Our dedication to fast turnaround times and quality workmanship ensures your equipment gets back into the field quickly, allowing you to continue serving clients who depend on your promptness during their most stressful moments.
Understanding the Importance of Professional Air Mover Repair
Air movers are major components in water damage restoration, mold remediation, and general drying applications, often running 24/7 during major restoration projects. When air movers fail during a job, it doesn’t just slow down the drying process; failed equipment can also disappoint clients, and damage your company’s reputation.
Many restoration professionals make the mistake of replacing units at the first sign of trouble, but professional air mover service and repair can extend equipment life, improve performance, and save you thousands in replacement costs. You deserve a service partner who treats your equipment with the same urgency you bring to your restoration emergencies.
Common Air Mover Issues That Require Professional Attention
Your air movers will face considerable wear and tear during regular operation. Some common issues they experience are:
- Unusual noises or vibrations during operation that signal potential motor problems or bearing failures
- Reduced airflow that hampers drying efficiency and extends job completion times
- Inconsistent performance where the unit works intermittently or shuts down unexpectedly
- Electrical issues, including tripped breakers, damaged cords, or non-responsive controls
- Motor overheating that leads to complete unit failure and potential safety hazards
Addressing issues promptly through professional air mover repair prevents minor problems from escalating into major equipment failures. Don’t wait until equipment completely fails in the middle of a critical job. Preventative maintenance and timely repairs will keep your operation running smoothly.
See Also: Neglecting Maintenance on Restoration Equipment
Air Mover Repair vs. Replacement: Making the Right Decision
Generally, air movers less than 5-7 years old with minor issues are excellent candidates for professional repair services; whereas units with multiple failed components or those that have already undergone several major repairs might be better replaced. The key is working with a partner like First Choice, who prioritizes your business interests over simply selling new equipment.
When you consult with our technicians about repair options, we consider:
- The unit’s age and service history for evaluating the remaining useful life
- The cost of repairs compared to the current replacement value
- The availability of parts for older models
- Your business’s current equipment needs and usage patterns
- The performance requirements for your specific restoration applications
Our consultative approach ensures you make equipment decisions that support both your immediate and long-term business goals. We see beyond the repair bench to understand how equipment decisions will impact your entire operation.
Why First Choice Drying Equipment Leads in Air Mover Repair
When comparing air mover repair services, experience and specialization matter. Unlike general repair shops that might work on everything from kitchen appliances to power tools, First Choice’s technicians are specialists in the unique demands of water damage restoration equipment.
Our repair team understands the critical nature of your business and the performance standards required for effective water damage restoration. You receive repairs from technicians who know exactly how these machines should perform in real-world restoration scenarios, not just in a workshop. Our specialized knowledge translates to more accurate diagnostics, more effective repairs, and equipment that performs reliably when you need it most.
Our Comprehensive Air Mover Repair Process
At First Choice Equipment Sales and Service, we’ve developed a systematic approach to air mover repair that ensures consistent, high-quality results. When you bring your equipment to us, you can expect:
- Thorough Initial Assessment: We will begin with a diagnostic to identify both obvious and hidden issues that might affect performance.
- Detailed Repair Estimate: Before any work begins, you’ll receive a clear, itemized estimate outlining the necessary repairs and associated costs, allowing you to make informed decisions.
- Professional Repairs Using OEM Parts: Our technicians use manufacturer-specified components and techniques to ensure repairs meet or exceed original performance specifications.
- Performance Testing: After repairs are completed, your air mover undergoes rigorous testing to verify it performs to industry standards under various operating conditions.
- Final Quality Inspection: Every repaired unit passes through quality checks before being returned to service, ensuring reliability when you deploy it on your next job.
Our approach to air mover repair eliminates guesswork and ensures that when your equipment leaves our facility, it’s ready for the demands of professional restoration work.
Our Commitment to Quality and Customer Satisfaction
At First Choice Drying Equipment, our reputation depends on the performance of equipment after it leaves our repair facility; that’s why we stand behind our air mover repair services with guarantees that reflect our confidence in our work. When we repair your equipment, you receive:
- 90-day warranty on all repair work performed
- 30-day satisfaction guarantee
- Detailed documentation of all services performed for your maintenance records
- Follow-up support if questions arise after your equipment returns to service
You deserve a partner who stands behind their work with meaningful guarantees, not just quick fixes and temporary solutions.
Read Also: Expert Repairs on Restoration Equipment with First Choice
How to Prepare Your Air Movers for Professional Repair
Taking these preparatory steps helps ensure efficient service and comprehensive repairs:
- Document the issues: Make notes about when and how performance problems occur, including any unusual sounds, smells, or behaviors.
- Clean external surfaces: Remove obvious dirt, debris, and water from the exterior to facilitate easier inspection.
- Gather service history: If available, bring records of previous repairs or maintenance to provide context for current issues.
- Check for physical damage: Inspect for cracks, dents, or damaged cords that might contribute to performance problems.
- Bring manufacturer information: Having model numbers and purchase dates helps technicians source the correct replacement parts.
Your preparation allows our technicians to focus immediately on diagnosing core issues so you can get your equipment back on the ground sooner.
If You Need Air Mover Repair, You Need First Choice Equipment Sales and Service
When your restoration business depends on reliable equipment, trust the specialists at First Choice Drying Equipment for professional air mover repair services. Our technicians understand the unique demands of water damage restoration equipment and provide repairs that extend equipment life while maintaining peak performance.
Don’t wait until equipment failure disrupts your projects and damages your reputation. Get in touch with First Choice Drying Equipment today to discuss your equipment repair and maintenance needs. Your restoration business deserves a reliable partner who keeps your business flowing, one perfectly functioning air mover at a time.
Jun 9, 2025
Portable dehumidifier repair services are vital to restoration companies seeking to maximize their investments and ensure equipment readiness in the event of a disaster. When water damage occurs in residential or commercial spaces, having fully functional dehumidifiers can mean the difference between a successful restoration job and a prolonged, complicated nightmare.
At First Choice Equipment Sales and Service, we understand that your dehumidifiers are the backbone of your restoration business. We are committed to helping you extend the life of your equipment through professional repair services, preventative maintenance, and proper usage techniques so your restoration business thrives.
Why Dehumidifier Repair Matters to Your Bottom Line
The financial impact of equipment failure during a restoration job can be substantial. If you’ve experienced a dehumidifier that quits mid-project, you know how troubling extended drying times and increased labor costs can be. Regular portable dehumidifier repair and maintenance not only prevent these costly disruptions but also significantly extend the lifespan of your investment.
Replacing a commercial-grade dehumidifier can cost anywhere from $1,000 to $3,000, while most dehumidifier repair services range from $150 to $500, making repairs a far more cost-effective option. With dehumidifier repair, you’ll see the savings directly impact your company’s profitability while maintaining the high standards your clients expect.
Read Also: Neglecting Maintenance on Restoration Equipment
Common Issues Requiring Portable Dehumidifier Repair
Refrigerant System Problems
If you notice that your unit is not collecting water or the coils are freezing up at normal operating temperatures, you’re likely experiencing refrigerant leaks or compressor issues that require professional portable dehumidifier repair.
Refrigerant leaks not only reduce your dehumidifier’s effectiveness but can also lead to total system failure if left unaddressed. You should never attempt to handle refrigerant issues yourself, as proper repair requires specialized equipment and certification due to environmental regulations. Professional repair companies, such as First Choice, can accurately diagnose the problem, seal any leaks, and recharge the system to optimal levels.
Electrical Component Failures
Electrical issues account for approximately 30% of all portable dehumidifier repair calls. Ironically, electrical components are sensitive to power surges and moisture exposure, the very conditions in which restoration equipment operates. You should not attempt to repair dehumidifier electrical issues on your own. Professional repair services from First Choice will include diagnostic testing of all electrical components, ensuring that your repaired equipment meets manufacturer specifications and safety standards.
Fan and Airflow Restrictions
Proper airflow is required for the efficient operation of a dehumidifier. The telltale signs of poor airflow include unusual noises, reduced water collection, or the unit running continuously without achieving target humidity levels. Regular cleaning of filters and coils should be part of your maintenance routine, but when mechanical issues arise with the fan system, portable dehumidifier repair is your best option.
When fan bearings wear out, or motors burn out, professional dehumidifier repair services from First Choice replace these components with high-quality alternatives that may even outperform the originals.
Water Removal System Defects
The condensate pump and drainage system are major components that require attention during portable dehumidifier repair. Condensate pumps typically last 2-3 years under heavy usage conditions before requiring replacement, but drainage hoses and connections may deteriorate faster due to constant moisture exposure.
If you’ve discovered water leaking around the unit or error codes indicating pump failure, you could end up with water damage at the job site, which is exactly what your restoration work aims to prevent. Professional repair services from First Choice include pressure testing of the drainage system, pump replacement when necessary, and verification that all water removal components function correctly before returning the restoration unit to service.
Preventative Maintenance: Reducing the Need for Portable Dehumidifier Repair
Creating an Effective Maintenance Schedule
Preventive maintenance is your first line of defense against costly dehumidifier repairs. A comprehensive maintenance schedule includes daily checks by operators, weekly cleaning procedures, monthly inspections of electrical components, and quarterly comprehensive servicing. Documenting these activities helps identify patterns of wear and potential issues before they cause equipment failure.
Training Your Team for Early Problem Detection
Your restoration technicians are the first to notice when equipment isn’t performing correctly. Unusual noises, reduced water extraction, error codes, or changes in amperage draw can all indicate developing issues that require attention.
By empowering your team with basic troubleshooting knowledge, you create a valuable early warning system for potential equipment failures. Your team should know how to perform basic testing, when to remove equipment from service, and how to document problems accurately for repair technicians. Having a partnership between your operators and repair professionals ensures that minor issues don’t develop into major repairs.
First Choice Drying Equipment: Your Partner in Portable Dehumidifier Repair
Our Comprehensive Repair Services
At First Choice Equipment Sales and Service, we’ve built our reputation on understanding the critical nature of your restoration equipment. Our dehumidifier repair services cover all major brands and models, with certified technicians who specialize in commercial-grade equipment.
Our repair facility features state-of-the-art diagnostic equipment that identifies issues that might be missed in basic inspections. You will receive detailed reports with every repair, documenting the problem, solution, and any recommendations for preventing future issues. This partnership approach helps you maximize equipment life and performance while minimizing unexpected downtime.
Repair or Replace: Expert Guidance When You Need It
Sometimes, portable dehumidifier repair isn’t the most cost-effective option, particularly for older units with multiple issues. You need honest, experienced advice about when to repair and when to replace. Our technicians provide this guidance based on equipment age, condition, repair history, and the availability of updates or improvements in newer models.
When dehumidifier replacement is the better option, we offer trade-in programs that recognize the value of your existing equipment. You’ll appreciate our transparent assessment process that considers both immediate costs and long-term operational savings. This consultative approach ensures you make equipment decisions that support your business goals and budget requirements.
See Also: Buy Used Restoration Equipment: Boosting Your Business Without Breaking the Bank
Get Professional Dehumidifier Repair Today with First Choice
Investing in professional portable dehumidifier repair services gives your restoration company a significant competitive advantage. Professional repair services protect your investment and ensure you’re always prepared to respond when disaster strikes.
Don’t leave your critical equipment in the hands of inexperienced technicians. First Choice Equipment Sales and Service stands apart with over two decades of specialized experience in the restoration industry and a 24-hour emergency repair hotline, ensuring you’re never left stranded during important jobs.
If you’re ready to extend the life of your restoration equipment and reduce costly downtime, call First Choice Equipment Sales and Service today or fill out our online form. Make the smart choice for your business by trusting the repair experts who truly understand the unique demands of the restoration industry.
May 15, 2025
In the competitive world of restoration, desiccant equipment repair is not just an occasional necessity; it’s a significant component of your business strategy that directly impacts your bottom line. When you’re facing tight project deadlines and demanding clients, the last thing you need is an equipment failure slowing you down.
At First Choice Equipment Sales & Service, we’ve seen firsthand how regular equipment maintenance can significantly boost your return on investment. With the proper upkeep of your equipment, you can transform your company’s reliability and profitability.
The Hidden Costs of Neglecting Desiccant Equipment Repair
When you postpone necessary maintenance on your desiccant dehumidifiers and other restoration equipment, you’re not saving money; you’re setting yourself up for larger expenses down the road. Neglected equipment doesn’t just break down more frequently; it operates less efficiently even when it’s running, costing you more in energy consumption and time.
Decreased Equipment Efficiency
Your desiccant dehumidifiers work by removing moisture from the air using specially designed desiccant materials. Over time, these systems collect dust, debris, and contaminants that restrict airflow and reduce efficiency. Without regular desiccant equipment repair and maintenance, you might notice:
- Longer drying times on job sites, extending project duration
- Higher energy costs as equipment works harder to achieve the same results
- Inconsistent performance that affects the quality of your restoration work
A desiccant dehumidifier operating at just 80% efficiency might seem acceptable, but it could add an extra day to your drying time. Multiply that across all your annual projects, and you’re looking at significant labor costs and reduced equipment availability for new jobs.
Premature Equipment Replacement
The average lifespan of quality desiccant equipment should be 7-10 years with proper maintenance. Without regular desiccant equipment repair, that timeline can shrink dramatically to just 3-5 years. When you consider that a commercial-grade desiccant dehumidifier can cost anywhere from $6,000 to $30,000, premature replacement represents a substantial unplanned expense.
Revenue Loss from Downtime
Perhaps the most significant cost comes from equipment failure during active projects. When your desiccant equipment breaks down on a job site, you face multiple challenges:
- Emergency repair costs, often at premium rates
- Project delays and potential contract penalties
- Damaged client relationships and reputation
- Lost opportunity costs when you can’t take on new projects
You can prevent downtimes and delays with desiccant repair services from First Choice Equipment Sales & Service.
Read Also: Neglecting Maintenance on Restoration Equipment
The ROI Benefits of Regular Desiccant Equipment Repair
When you implement a proactive desiccant equipment repair program, you’re making a strategic business decision that delivers returns in multiple ways:
Extended Equipment Lifespan
Consistent maintenance significantly prolongs the useful life of your desiccant equipment and directly impacts your ROI.
For example, if a $15,000 desiccant dehumidifier lasts 10 years instead of 5 years due to proper maintenance, your annual depreciation cost drops from $3,000 to $1,500 per year, saving your bottom line.
Enhanced Performance and Productivity
Well-maintained equipment operates better. When your desiccant dehumidifiers are operating at peak efficiency, you’ll notice:
- Faster drying times, allowing you to complete jobs more quickly
- More consistent performance, delivering better results for your clients
- Reduced energy consumption, lowering your operating costs
Performance improvements will translate to higher productivity, allowing you to handle more jobs with the same equipment inventory, therefore boosting your revenue potential.
Predictable Maintenance Costs vs. Unpredictable Repairs
When you schedule regular desiccant equipment repair and maintenance, you transform unpredictable emergency expenses into planned, budgeted costs, allowing for:
- Better cash flow management
- More accurate job costing and estimating
- Reduced financial stress during busy seasons
Most restoration companies find that their annual maintenance costs are 30-50% lower than what they previously spent on emergency repairs and lost productivity.
Strategic Approaches to Desiccant Equipment Repair
Understanding the importance of maintenance is one thing. Implementing an effective program is another. Here are proven strategies to maximize your maintenance ROI:
Establishing a Preventative Maintenance Schedule
The foundation of effective equipment management is a well-designed maintenance schedule. For desiccant equipment repair, consider:
- Monthly inspections of filters, airflow systems, and desiccant wheels
- Quarterly comprehensive performance assessments
- Annual professional service from certified technicians
Your schedule should be documented and tracked, with clear responsibilities assigned to specific team members. Digital maintenance management systems can help automate reminders and track maintenance history.
Professional Service Partnerships
Developing a relationship with qualified service providers like First Choice Equipment Sales & Service gives you access to specialized expertise. Professional technicians bring:
- Manufacturer-specific knowledge and training
- Specialized diagnostic equipment
- Access to genuine replacement parts
- Documentation of service for warranty purposes
The best service partnerships are proactive, not just reactive. Your service partner should help you develop maintenance protocols and provide advice on proper equipment handling.
Long-Term Strategic Benefits of Proactive Desiccant Equipment Repair
Beyond immediate financial returns, a commitment to equipment maintenance offers strategic advantages that position your restoration business for long-term success:
Competitive Differentiation
In a market where companies compete primarily on price, reliability becomes a powerful differentiator. When you can confidently promise clients that your equipment won’t cause downtimes, you create a compelling reason to choose your services over competitors.
Enhanced Financing Options
Lenders and equipment financing companies often offer better loans for businesses with documented maintenance programs. Well-maintained equipment represents lower risk and higher residual value, potentially qualifying you for:
- Lower interest rates on equipment loans
- More favorable lease terms
- Higher approved financing amounts
- Extended warranty options
Scalability Advantages
As your restoration business grows, a systematic approach to desiccant equipment repair makes scaling easier. New team members can be integrated into established maintenance procedures, ensuring consistency as you expand. Having operational discipline often distinguishes businesses that successfully grow from those that struggle with expansion.
See Also: Expert Repairs on Restoration Equipment with First Choice
Desiccant Equipment Repair as a Profit-Generating Investment
When you shift your perspective from viewing maintenance as a necessary cost to seeing it as a profit-generating investment, you transform your approach to equipment management. Regular desiccant equipment repair prevents downtimes and actively contributes to your business success through improved efficiency, extended equipment life, and enhanced project outcomes.
The restoration companies that thrive long-term are those that recognize this reality and build maintenance excellence into their operational DNA. Staying proactive with preventative maintenance will position your business to achieve the highest return on investment for your equipment.
Take the Next Step in Maximizing Your Equipment ROI with First Choice
Ready to transform your approach to desiccant equipment repair? First Choice Equipment Sales & Service offers comprehensive maintenance programs specifically designed for restoration businesses.
Our technicians understand the unique demands of restoration equipment and can help you implement a maintenance strategy that maximizes your ROI.
With over 15 years of industry experience, we’ve saved clients thousands in replacement costs through our proactive maintenance approach, and our 24/7 emergency support ensures your equipment stays operational during critical restoration projects.
Contact First Choice Equipment Sales & Service today by filling out our online form or giving us a call. Our experts are standing by to discuss how we can help extend the life of your restoration equipment and improve your bottom line!
Apr 28, 2025
If you’re struggling with faulty equipment slowing down your projects, expert repairs on restoration equipment could be your solution. Restoration equipment repair can save you time, money, and frustration when facing tight project deadlines.
At First Choice Drying Equipment, we understand that your restoration tools are the lifeblood of your business, and any downtime can significantly impact your ability to serve clients effectively. Our company is dedicated to becoming the leading expert in comprehensive restoration equipment repair services across Colorado and Oklahoma.
Why Professional Restoration Equipment Repair Matters
You depend on your equipment day in and day out, often in challenging environments that put significant stress on even the highest quality machines. Over time, wear and tear from restoration projects will lead to reduced performance or complete breakdowns if not properly addressed.
Expert repairs on restoration equipment from certified technicians can extend the lifespan of your equipment, protecting your investment and ensuring reliability when you need it most.
See Also: Neglecting Maintenance on Restoration Equipment
Comprehensive Restoration Equipment Repair Services at First Choice
At First Choice Drying Equipment, we take pride in offering a complete suite of restoration equipment services and repairs. Our skilled technicians provide expert repairs on restoration equipment across a wide variety of equipment brands and models:
Desiccant Repair: Restoring Optimal Performance
Our technicians are thoroughly trained in desiccant dehumidifier repair, with the knowledge and skills to diagnose issues accurately and implement effective solutions.
Our desiccant repair service includes comprehensive diagnostics, thorough cleaning of all components, replacement of worn or damaged parts, and complete system testing to ensure everything functions properly.
Portable Dehumidifier Repair: Keeping Your Essential Tools Running
Our portable dehumidifier repair services address common issues like refrigerant leaks, compressor failures, fan problems, and control board malfunctions.
Our technicians stay up to date with the latest repair technology and techniques for LGR dehumidifiers, conventional refrigerant units, and specialty models, allowing us to provide comprehensive expert repairs on restoration equipment, renewing it to original condition.
Air Mover and Fan Repair: Maximizing Airflow Efficiency
Our air mover and fan repair services will address every component of an air mover, from motor issues and electrical problems to housing damage and control failures.
We work on all styles, including axial fans, centrifugal air movers, and low-profile units.
With our expert repairs on restoration equipment, you can expect thorough diagnostics, professional repairs, and comprehensive testing before your equipment is returned for service.
Your air movers will leave our shop ready to deliver the powerful, reliable airflow you need for effective restoration work.
Air Scrubber Repair: Ensuring Clean Air Operations
Our air scrubber repair services cover the full range of issues that scrubbers can experience, including filter systems, motor problems, housing damage, and electrical malfunctions.
We work with both standard and HEPA-filtered models to ensure your air quality control equipment performs reliably.
Our technicians understand the role that air scrubbers play in containment strategies and particulate removal. When providing expert repairs on restoration equipment, we thoroughly inspect all components, address any identified issues, and test the unit’s airflow and filtration efficiency before returning it to service.
Medical Grade Portable Air Scrubber Repair: Specialized Expertise
For restoration companies that work in healthcare facilities or other sensitive environments, medical-grade air scrubber repair is recommended.
Our technicians have the training and experience necessary to work on medical-grade scrubber units, ensuring that your air scrubbers meet the exacting standards required for hospital environments.
Our medical-grade air scrubber repair service includes thorough inspection of all components, verification of proper filtration efficiency, and comprehensive testing to ensure that the unit meets all applicable standards.
We pay particular attention to the integrity of HEPA filtration systems and make sure that every safety feature is functional, ensuring that your equipment is ready for the most demanding environments.
The First Choice Advantage in Restoration Equipment Repair
When you choose First Choice Drying Equipment for expert repairs on restoration equipment, you’re partnering with a company that genuinely understands the restoration industry.
We have unique insight into how these tools are used in real-world situations, allowing us to address the underlying cause of your equipment failure.
Expert Technicians with Industry Knowledge
Each technician undergoes continuous training to stay current with the latest equipment models and repair techniques. Our commitment to this ongoing education ensures that we’re always prepared to work on both legacy equipment and the newest technology in the restoration industry.
When you bring your equipment to First Choice, you can be confident that you’re getting expert repairs on restoration equipment.
Convenient Expert Repairs on Restoration Equipment for Busy Restoration Professionals
We’ve developed service options designed to minimize disruption to your business.
For clients with 20 or more items needing service, we offer free pickup and delivery within a 250-mile radius of our Colorado and Oklahoma locations.
Our convenient service allows you to maintain your focus on current projects while we take care of your equipment needs.
For urgent repair situations, we offer priority service options to get your equipment back in service as quickly as possible.
Our team will maintain the highest quality standards, ensuring that rush repairs don’t compromise the longevity or reliability of your equipment.
Certified Warranty Service for Major Brands
First Choice Drying Equipment is a certified provider of warranty service for Phoenix and Xpower equipment. Manufacturer certifications reflect our commitment to meeting the highest standards of repair quality and technical expertise.
When you bring your warranty-covered equipment to us, you can be confident that expert repairs on restoration equipment will be performed to manufacturer specifications using genuine parts.
Our certified status also means we have direct access to technical support and parts from the manufacturers, allowing us to complete warranty repairs efficiently and effectively.
Beyond Repairs: Your Complete Restoration Equipment Resource
While our restoration equipment repair services are central to our business, First Choice Drying Equipment offers a comprehensive range of services for restoration professionals. We’re your one-stop resource for all equipment needs, from sales and rentals to maintenance and technical advice:
Quality Used Equipment Sales
Sometimes, the cost of expert repairs on restoration equipment can make replacement a more economical option.
We offer a selection of quality used restoration equipment at competitive prices.
All our used equipment undergoes thorough inspection and servicing before sale, ensuring that you’re getting reliable tools at a fraction of the cost of new equipment.
Read Also: Buy Used Restoration Equipment: Boosting Your Business Without Breaking the Bank
Equipment Rental Options
For temporary capacity needs or specialized project requirements, our rental program provides access to well-maintained restoration equipment without the commitment of purchase.
At just $50 per day plus shipping, our rental options allow you to scale your equipment resources to match your current workload, ensuring that you always have the right tools for the job.
Trust First Choice for Expert Repairs on Restoration Equipment
When your restoration equipment needs professional attention, First Choice Drying Equipment delivers the expertise, convenience, and quality you demand.
Don’t let equipment issues compromise your restoration projects or damage your professional reputation.
Partner with First Choice Drying Equipment for expert repairs on restoration equipment to keep your tools performing their best.
Our commitment to quality equipment repairs and exceptional customer service has made us the preferred equipment partner for restoration professionals across Colorado and Oklahoma.
Reach out to First Choice to discuss your specific restoration equipment repair needs or to schedule service. Let us help you keep your restoration business running at peak efficiency with expert equipment repair services you can trust!
Feb 24, 2025
You already know that disaster restoration is a demanding industry that requires specialized equipment to dry, clean-up, repair, and restore damaged properties. Often, in the rush to make the next buck, we fail to properly maintain this equipment. We also know, (or should know) that proper maintenance is crucial for ensuring safety, reliability, and efficiency. Regular upkeep prevents breakdowns, extends machinery lifespan, and reduces costly repairs. However, when maintenance is neglected, both the job and the equipment suffer, leading to operational inefficiencies, financial losses, and even potential safety hazards.
Equipment Breakdown and Downtime
One of the most immediate consequences of improper maintenance is the increased likelihood of equipment breakdown. Restoration projects operate under strict timelines, and an unexpected failure of a dehumidifier, air scrubber, or water extractor can significantly delay progress. When equipment fails, jobs take longer to complete, leading to frustrated customers and potential loss of business. Additionally, downtime forces restoration companies to rent or purchase replacement equipment, which adds unexpected costs that could have been avoided with some simple, easy maintenance.
Even a bigger headache is when OSHA or other inspectors find frayed or cut cords on your equipment. It’s not talked about much, but cut or damaged extension cords are illegal to use and can cause injury or death. Cutting the ground plug off the end is certainly a no-no.
Increased Repair and Replacement Costs
Equipment that is not properly maintained deteriorates faster, leading to costly repairs and, in some cases, complete replacement. For example, failing to clean air filters in dehumidifiers and air scrubbers can cause motors to overheat, resulting in expensive repairs. Similarly, ignoring oil changes or lubrication needs in heavy machinery leads to mechanical failures. So many times, we fail to follow diesel generator suggestions for changing the oil at the right intervals. Most have 50 hours as a recommendation to change the oil and filter. Incurring minor maintenance costs help prevent spending thousands of dollars on major repairs or new equipment purchases, impacting profitability. With diesel generators costing $50,000 or more, spending an hour and $100 seems logical and appropriate.
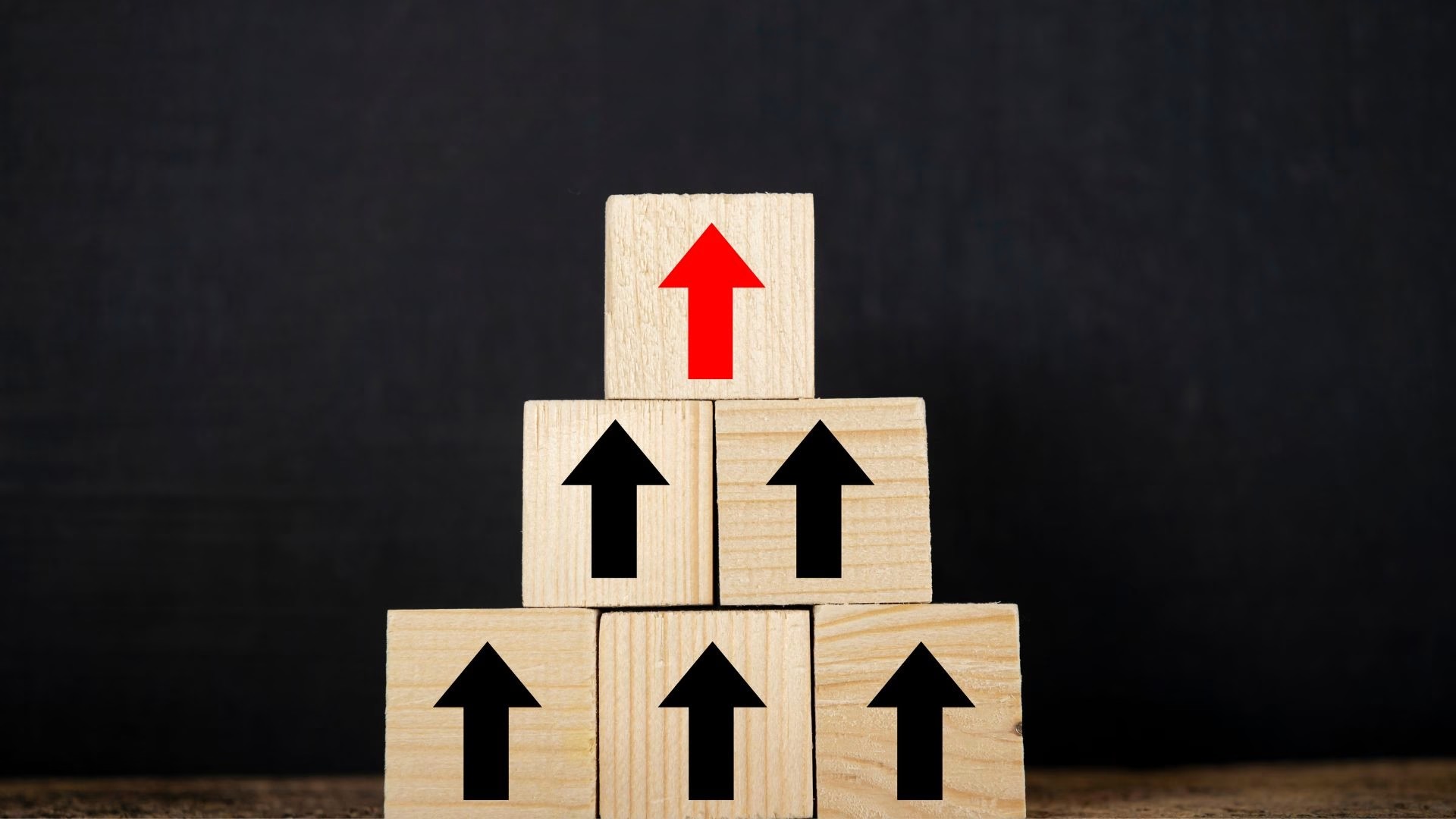
Reduced Efficiency and Performance
Disaster restoration equipment is designed to operate at peak efficiency, ensuring that water extraction, drying, and air purification processes are completed as quickly and effectively as possible. When maintenance is neglected, machines work harder to achieve the same results, leading to increased energy consumption and reduced performance. A clogged vacuum filter, for instance, forces an extractor to use more power, which not only increases electricity costs but also reduces the machine’s ability to remove water effectively. Poorly maintained equipment can extend the time required to complete restoration projects, which negatively impacts customer satisfaction and company reputation. Something as simple as cleaning fan blades, checking for damaged cords, plugs, and switches can make all the difference. Even taking a few moments to lubricate the motor can help.
Safety Risks and Liability Issues
Failure to maintain disaster restoration equipment can pose serious safety risks to workers and customers. Malfunctioning electrical equipment increases the risk of short circuits and fire hazards, while mechanical failures in heavy-duty machines can lead to accidents and injuries. Additionally, improper maintenance of air scrubbers and dehumidifiers can lead to mold growth and poor indoor air quality, putting both employees and customers at risk. When accidents or health hazards occur due to poorly maintained equipment, restoration companies can face legal liabilities, lawsuits, and damage to their credibility. Making sure coils in portable dehumidifiers are clean, and changing the filter as needs will ultimately pay big dividends.
Compromised Job Quality and Customer Dissatisfaction
The success of disaster restoration projects relies on the ability to restore properties effectively and efficiently. Poorly maintained equipment leads to subpar results, such as incomplete water extraction, lingering odors, and insufficient drying, which can cause long-term damage to properties. Customers who experience inadequate service due to equipment failures are less likely to trust the company again and may leave negative reviews or complaints, damaging the business’s reputation. We know that Word-of-mouth referrals are valuable in the disaster restoration industry, and dissatisfied customers can drastically impact future business opportunities.
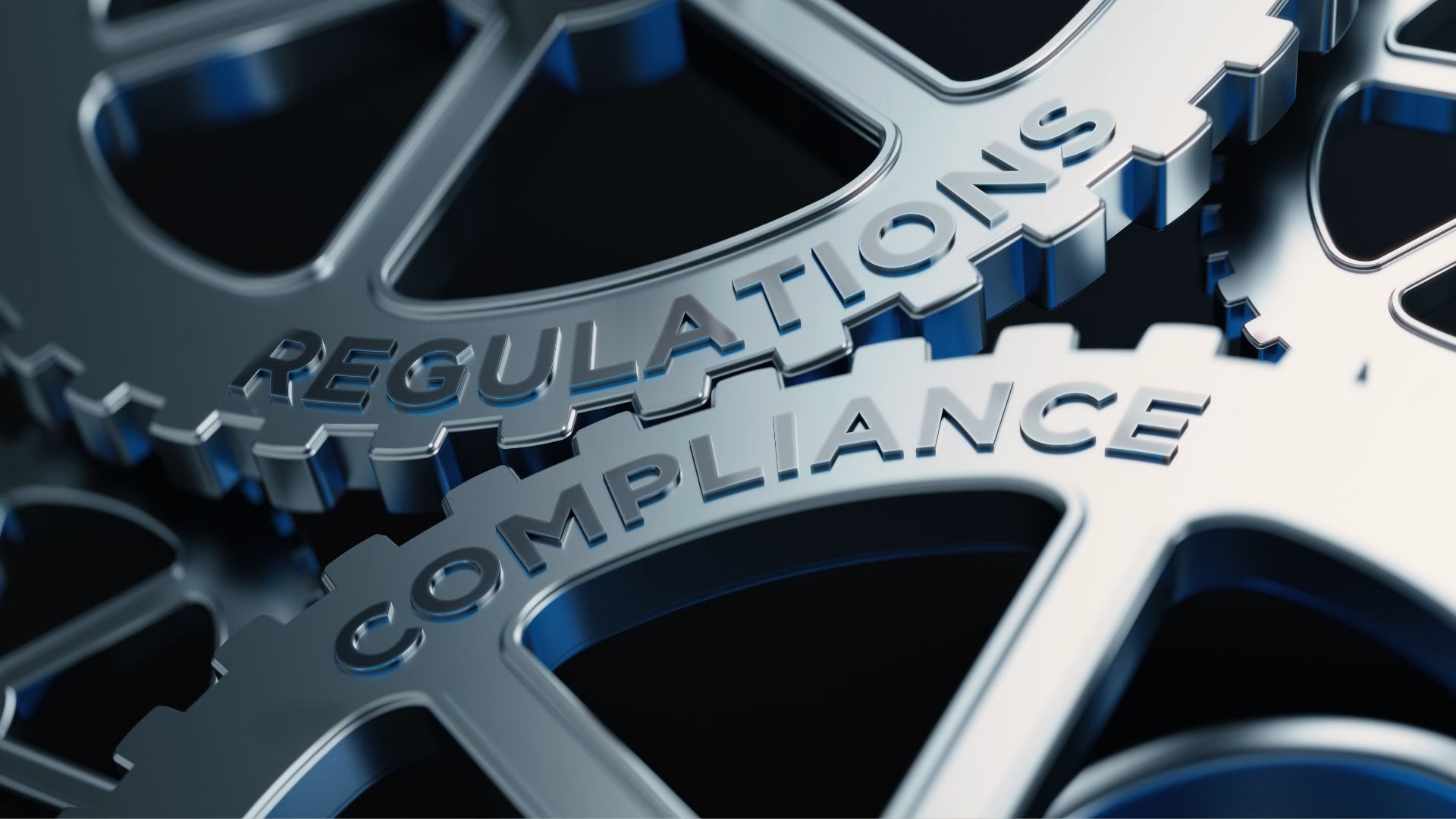
Compliance and Insurance Implications
Most disaster restoration projects must adhere to industry standards and insurance requirements. Neglecting equipment maintenance can result in non-compliance with regulations set by organizations such as the Institute of Inspection, Cleaning and Restoration Certification (IICRC) or the Occupational Safety and Health Administration (OSHA). Additionally, insurance providers could refuse claims related to equipment failures if maintenance records show negligence, leading to financial burdens for the company.
Regular maintenance of disaster restoration equipment is essential for ensuring safety, efficiency, and profitability. Neglecting maintenance leads to equipment failures, increased costs, safety risks, and dissatisfied customers, all of which can severely impact business operations. By implementing routine inspections, timely repairs, and proper cleaning protocols, disaster restoration companies can avoid costly setbacks and provide reliable services. Investing in preventive maintenance not only extends the lifespan of essential equipment but also contributes to a safer and more efficient work environment.
First Choice Equipment Sales and Service sells high-quality drying equipment for construction, restoration, and property renovations. Buying your used equipment can help you upgrade and improve your inventory. If you are trying to sell used equipment, please call us for an estimate. We have completely refurbished used equipment.
Written by: Beth Hinton and D Wagner